As electric vehicles (EVs) gain popularity, the demand for better charging solutions is increasing. This emphasizes the critical role of Printed Circuit Board (PCB) Assembly in producing efficient EV chargers. PCB Assembly involves creating essential components required for effective EV charging systems. These specially designed circuit boards ensure that EV chargers operate reliably and safely. In this article, we will discuss why EV Charger PCB Assembly is Important and how it supports the functionality and Better performance of electric vehicle chargers. The process includes meticulous design, precise manufacturing, and rigorous testing, guaranteeing that the chargers meet high standards of safety and efficiency, ultimately enhancing the overall EV charging experiences.
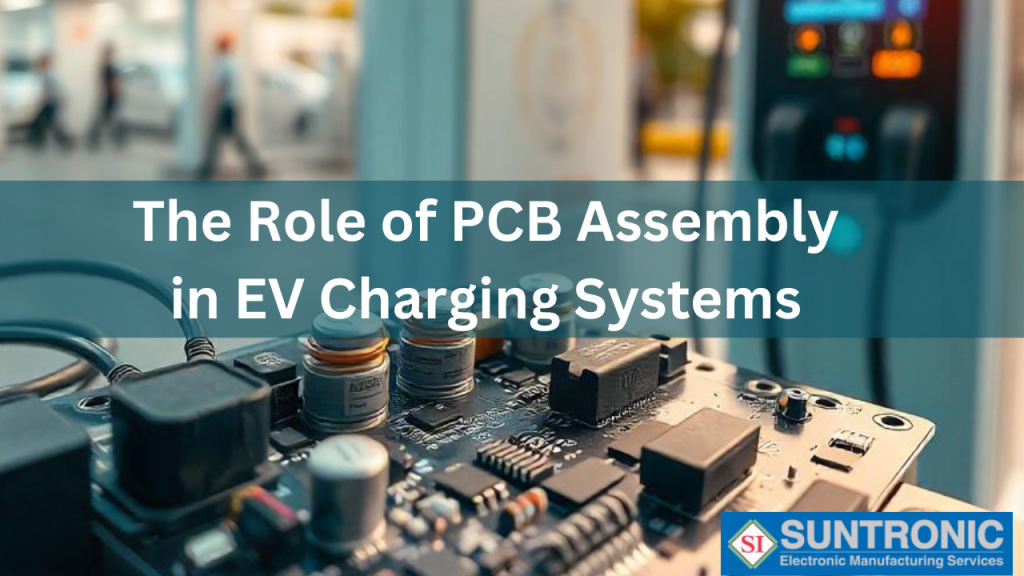
PCB Assembly is similar to constructing the nervous system of an EV charger, comprising intricate electronic components carefully assembled onto a circuit board. This process involves placing components Like capacitors, resistors, and microchips onto the board, creating a functional system. Accuracy and quality are paramount to guarantee the charger’s safety and efficiency.
What is EV Charger PCB Assembly?
EV Charger PCB Assembly involves creating specialized printed circuit boards for electric vehicle chargers. This process includes careful design, precise manufacturing, and thorough assembly to ensure high performance and safety. Each PCB is rigorously tested to meet safety and compliance standards. These PCBs are important l for the reliable operation of EV chargers, ensuring they function efficiently and effectively. The Thorough approach in every Single step guarantees the production of high-quality PCBs, providing safe and reliable charging for electric vehicles.
Key Components of EV Charging Systems
EV charging systems consist of several core components, each playing an important role in the overall functionality:
- Power Modules: Convert and manage electrical power.
- Communication Modules: Enable communication between the vehicle and the charging station.
- Control Units: Oversee the management of the charging process.
- Safety and Protection Circuits: Ensure the system operates safely and protects against faults.
PCBs integrate these components into a cohesive system, ensuring seamless operation and efficient power management.
PCB Design Considerations for EV Charging Systems
Designing PCBs for EV charging systems involves critical considerations:
- Thermal Management: High-power charging generates significant heat, managed using thermal vias and heat sinks.
- Signal Integrity and Power Distribution: Careful layout design maintains signal integrity and minimizes power losses.
- Durability and Reliability: High-quality materials and robust designs ensure PCB longevity.
- EMI/EMC Compliance: Minimizing EMI and ensuring EMC prevents malfunctions and ensures regulatory compliance.
Advances in PCB Technology for EV Charging Systems
The evolution of PCB technology has brought significant advancements benefiting EV charging systems:
- High-Density Interconnect (HDI) PCBs: Allow for higher component density, improving performance and enabling more compact designs.
- Flexible and Rigid-Flex PCBs: Offer greater design flexibility, allowing for innovative form factors and improved space utilization.
- Embedded Components and Advanced Materials: Embedding passive and active components within the PCB can enhance performance and reliability. Additionally, advanced materials such as high-temperature laminates improve durability and thermal management.
Challenges in PCB Assembly for EV Chargers
PCB assembly for EV chargers poses several unique challenges due to high power requirements, safety considerations, and reliability demands. Here are some key challenges faced:
- High Power Density: EV chargers need to deliver high power levels efficiently, requiring careful layout design and thermal management.
- Thermal Management: Efficient heat dissipation is crucial to prevent overheating, which can degrade components and reduce reliability.
- High Voltage Handling: Proper insulation, clearance, and creep age distances on the PCB are essential to meet safety standards and prevent electrical arcing.
- EMI/EMC Compliance: Designing PCBs with proper shielding, filtering, and grounding is crucial to minimize EMI emissions and ensure compatibility with other electronic devices.
- Reliability under Harsh Environments: PCB components and materials must be selected carefully to ensure reliability under outdoor or harsh environmental conditions.
- Safety Standards Compliance: PCB designs need to incorporate safety features like overcurrent protection, overvoltage protection, and fault detection mechanisms.
The Future of PCB Assembly in EV Charging Systems
Upcoming developments in PCB assembly will prioritize efficiency, sustainability, and scalability. Innovations like advanced materials, modular designs, and intelligent charging management systems will streamline assembly processes, catering to the increasing demand for EV charging framework. The future promises faster, safer, and more sustainable solutions for EV charging.
Conclusion
PCB Assembly forms the foundation of dependable and efficient EV charging networks, guaranteeing secure and stable power supply for electric vehicles. Consistent innovation, adherence to stringent standards, and industry collaboration are essential to propel the development of sustainable EV charging infrastructure. Embracing these principles ensures that EV chargers meet the evolving needs of electric mobility while minimizing environmental impact and enhancing user experience.
Related Blogs:
- How to Deal with Heat Dissipation in PCB Assembly
- The Importance of Impedance Control in PCB Assembly
- Troubleshooting PCB Failures: How PCB Testing Helps Identify Issues
Face Shield Mask,Welding Face Shield,Safety Shield,Protective Face Shield
Xuzhou Xinbaisheng Protective Equipnent Co., Ltd. , https://www.xinparkson.com